Experience
proved that design quality is proportional to the precision
of the small details development.
That design correctness can be achieved only with an extensive
knowledge, with understanding of all
designed parts, and by employing effective design methods
with the proper design process.
Good quality of any product and good results of any activity
requires the proper process. Cooking,
flying the airplane, launching the rocket, building a
house, driving a car, wedding ceremony and anything
else requires the right process, since results of any
operation depend on the selected sequence of actions.
Most of organizations indicate three to eight product development
stages, and generally design process
can be described by four main phases;
Phase 1 - Concept development for the product functions
and its form
Phase 2 - Assembly components development with manufacturing
process planning
Phase 3 - Detailed features creation for operational functions,
structure, mechanisms and attachments
Phase 4 - Design validation of the product performance and
durability, and product design perfecting
All product development phases create together one continuous
design process and the only visible
transition between those phases is a step of design verification.
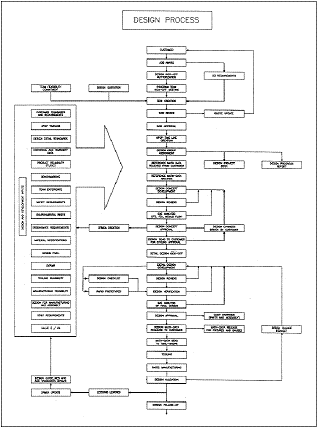
Each of those design phases has own subsequent detailed
sub-steps, and knowledge of those steps
greatly helps with the proper design development management
including design progress tracking as well.
Most of the product development teams prefer to control
design quality with methods that are combinations
of the three general practices;
A - Experts confirmation - Product design piloting and reviews
with experts representing various fields of
----- the product creation
and its functional use; i.e. materials, tooling, manufacturing,
quality, safety,
----- ergonomics, packaging,
etc.
B - Structured Methods - Design development by solving design
problems with the specific techniques
----- and design verification
with those methods including; FMEA,
DFMA,
QFD,
VE/VA,
DOE, Fishbone,
8D,
----- and systems as Six
Sigma or TRIZ.
C - Guidelines & Checklist - Design creation by applying
the verified registered knowledge as the design
----- criteria and as the
design evaluation vs. those criteria.
Each of these three approaches has different power of the
design problems detection and those design
problems elimination.
Expert knowledge
as observations indicate is usually possessed just
by few top specialists in most of
organizations. Their knowledge of the product and their
techniques of design-thinking are not recorded
even by companies specialized in development and manufacturing
of those particular products.
Most of the expert's knowledge is difficult to record because
of a huge number of details and because
those individuals possess more than just static memorized
knowledge. They have ability of creating the
optimal solutions for most of design related problems.
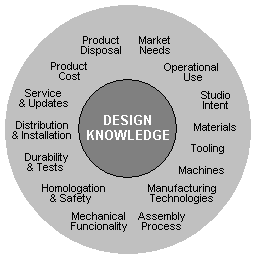
Good expertise used from the beginning of the product design
results in a good quality of the product, and
lack of expertise usually relates to a poor design with
errors. That is maybe why it has been observed that
attempts of moving product design from specialized suppliers
to the less-expensive companies or to own
in-house design teams resulted in design difficulties
and in products problems.
Because of that, the benchmarking is regularly used as
the main source of the safe design solutions with
with assumption of the correctly designed benchmarked
parts that represent the best validated knowledge.
Furthermore, if preferred own solution is not found in
benchmarking then it may be discarded as too risky
without awareness that copying of some benchmarked solutions
to the other products can be risky as well.
Structured product development
methods are preferred by big organizations
but unfortunately most of
those methods focus on the narrow fields of the design
knowledge, so multiple methods should be used
simultaneously to address all aspects of the product design
during its development. That can be time
consuming for designers. Thus, most of those methods are
not so practical when various and frequent
design decisions must be made quickly.
There are many existing
product
development methods and descriptions of those methods
can be found in
multiple
publications;
Design guidelines
and product development criteria are usually created based
on lessons learned and
other multiple sources including knowledge of experts
and verified design solutions from benchmarking.
Development of the design guidelines is quite elaborative
task and that document should be formed as
a flexible for the subsequent updates with the new design
knowledge. The best design guidelines are if
combined to one very extensive document with an index of
design features and with descriptions of the
respective design solutions.
Experience confirmed that those
detailed design guidelines and related design checklists
are powerful,
practical and easy to use tools for achieving significantly
high quality of the product.
Functional description
If the unique product must be designed with no existing
design guidelines then one of the most effective
ways to understand that new product and its details is
to look at all parts and all features from the function
point of view. Everything has a function and everything
should have a function.
Functions are described with two words; with an active
verb (what is being done) and with a noun
(object or characteristics of the applied action), i.e.;
locate component, reduce wear, prevent deformation,
eliminate rattle, provide attachment, ...etc.
The functional description of the product, its components
and details helps to make the optimal design
decisions and helps to eliminate design waste of creating
no-function components or details. For that
reason design correctness should be verified with questions
for functionality of each designed element;
Q1 - What are expected functions of the product, component,
feature and detail?
- Market needs and trends
- Operational use functions
- Studio intent of appearance and perception
- Materials properties and compatibility
- Tooling, fixtures and gages
- Manufacturability (requirements/guidelines for manufacturing
process)
- Assembly (both manual and automation)
- Mechanical functionality of the structure (static and
dynamic)
- Durability/reliability and specified tests
- Homologation and safety standards
- Distribution and installation
- Service and updates
- Design simplicity and product cost
- Product discarding and environment
Q2 - What design solutions are available for the required
functions of the product?
Q3 - If all required functions can be achieved with the
proposed idea or different solution is needed?
Q4 - What is the function of already designed component/detail
and if that component/detail should exist?
The entire design can be verified and most of the product
problems can be detected with the above questions
during the design development.
Recommendation
Regardless of the method preferred for the design quality
control, it is highly recommended to evaluate the
entire design thoroughly at least at the end of each design
phase and before its final release to the tooling.
|